In the 21st century, large portions of the U.S. are becoming more drought-prone. An estimated 53 million people (about twice the population of Texas) are living in drought-affected areas.” This escalating drought situation necessitates that electric utilities account for these changing conditions at existing sites and design future substations that will remain within the site safety criteria specified in the IEEE standards.
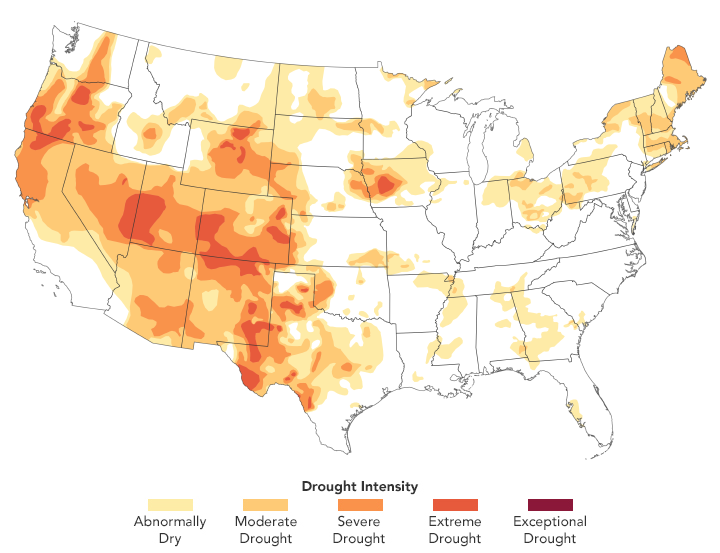
According to NASA, more than 93 percent of the land area in Utah, Colorado, Nevada, and New Mexico is in some level of drought.
For example, certain areas across the country use aquifers and ground wells to augment the efficacy of their substation ground grids and lower the site ground resistance. These design options rely on the grounding components penetrating wet conditions. However, under severe drought conditions, the groundwater depth can increase, and the grounding elements are no longer immersed in the wet conditions. This change could dramatically impact the site’s overall safety. Electric utilities need to be aware of sites where safety margins could be compromised, resulting in unsafe conditions. Owners should consider re-testing existing sites of concern and re-evaluating grounding designs to ensure compliance with the relevant standards under adverse conditions.
Case Study
At one substation site, during normal weather (moisture) conditions, we measured an upper soil layer resistivity at 145 Ohm-meters, a top layer thickness of 31 feet, and a ground grid impedance of 2.9 Ohms. After an extended drought, we remeasured the soil resistivity. The moisture in the upper layer had decreased, and the upper layer resistivity had increased dramatically to 1,002.8 Ohm-meters for the top 12 feet with an increased ground grid impedance to 3.35 Ohms – a 15% change. If the grounding design was completed with a safety margin of 15% or less or the safety margin has eroded over the years due to other site changes, this could present safety issues with increased touch and step potentials and an increased overall grid impedance value.
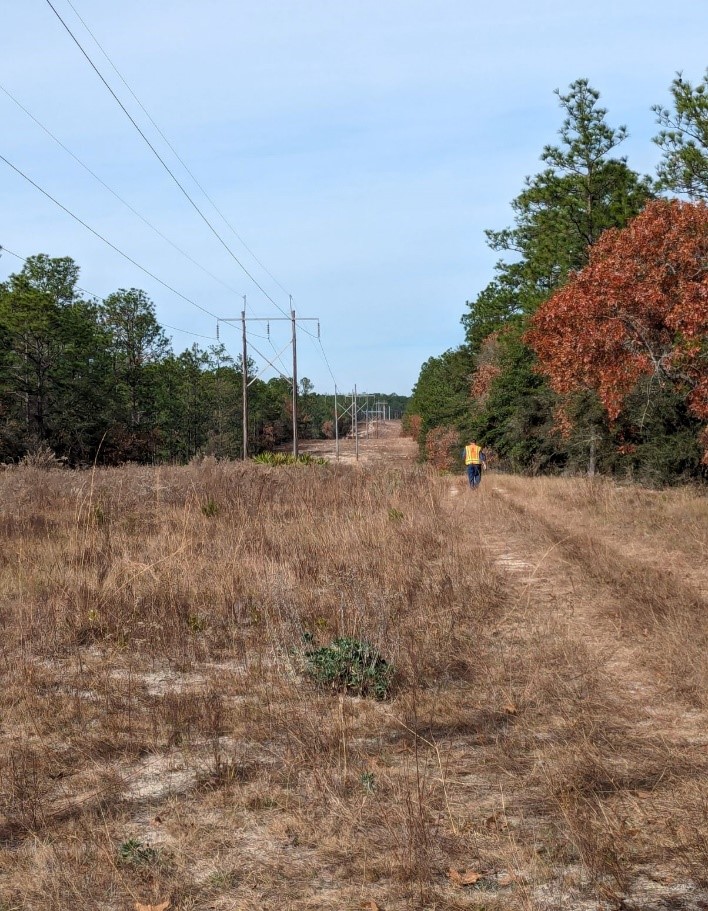
Poor native soil conditions combined with dry soil can make soil resistivity testing extremely difficult.
For other sites across the country with poor native soil conditions, even performing soil testing becomes extremely difficult. One of our clients was plagued by poorly performing transmission lines, typically under lightning storm conditions, and we suspected high tower footing resistance. Performing Wenner method soil tests with hand-held portable equipment (limited current output) proved to be impossible. We used specialized (higher current output) grounding test equipment and still had to go to extreme lengths to obtain valid site data. This included adding and driving many extra-long test probes (rods) and augmenting the probe connections to native soil with water to improve the rod-to-soil contact. We were able to get soil resistivity measurements proving the footing resistance to be high and designed suitable remediation at each transmission pole to improve the situation.
Changing soil conditions, while usually not an issue in the short term, can become a site safety issue if long-term changes in the soil moisture result in higher upper-layer soil resistivity. Ground grid designs and safety margins must be robust enough to withstand soil resistivity increases. Areas of the country at risk for long-term drought should consider retesting and reevaluating soil resistivity, ground grid impedance, and touch and step potential to determine if existing sites are still safe or if remediation needs to be implemented. For new installations, increased safety margins should be employed to cover soil changes and other typical site factors, such as growth and increased fault current. In case of doubt, field testing can help to confirm whether a site remains safe for personnel and equipment.
Hilton Mills contributed to this article. With more than 30 years of experience, Hilton is an industry thought leader in grounding theory, testing methodology, design, and assessments. He appears as a speaker at various industry conferences, and provides on-site training on protective relay application and grounding system design and testing.